Predictive maintenance is an increasingly popular approach to managing field service operations. By using predictive models and data-driven analysis, field service organizations can identify potential problems before they occur and proactively plan for the future.
This type of proactive management helps companies improve efficiency, reduce costs, extend equipment life cycles, and increase customer satisfaction. In this article we will discuss the advantages of implementing predictive maintenance in a Field Service Management Software system.
Improved Equipment Performance
Predictive maintenance is an invaluable asset for any field service management software. It enables companies to anticipate and prevent equipment breakdowns, thereby improving overall performance. With predictive maintenance, potential problems can be identified before they result in costly repairs or downtime.
This allows businesses to use their resources more efficiently and effectively, which leads to improved equipment performance. Companies are able to save money on repair costs by proactively addressing issues with their machinery, as well as avoid delays that may be caused by unexpected malfunctions or breakdowns of equipment.
Predictive maintenance also helps reduce the need for manual inspections that require costly labor and time away from other important tasks in the field service industry. By utilizing predictive maintenance capabilities within a field service management software solution, businesses will be able to identify potential problems sooner rather than later and take action accordingly – allowing them to maximize their profits while keeping costs down at the same time.
Increased Uptime & Efficiency
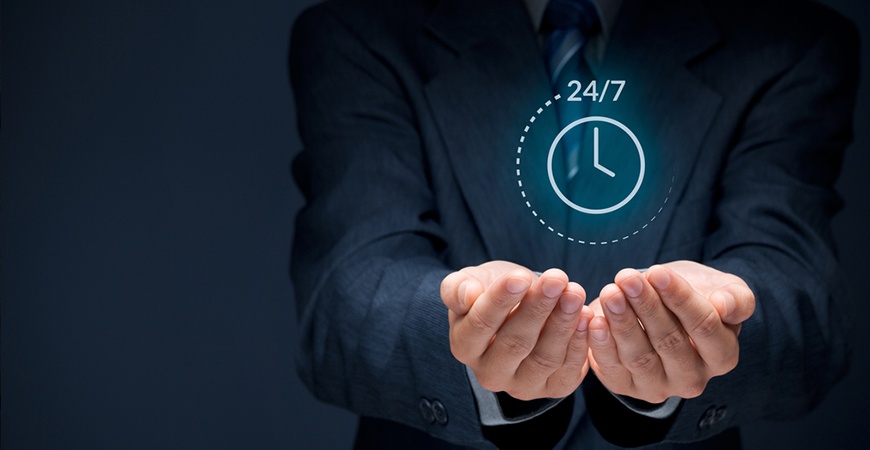
Predictive maintenance is a powerful tool for field service management software, allowing users to take proactive measures which result in increased uptime and efficiency. By anticipating potential issues before they arise, predictive maintenance prevents costly disruptions from occurring and keeps operations running smoothly.
This helps eliminate the need for emergency repairs and significantly reduces downtime costs. Predictive maintenance also allows for more accurate scheduling of preventive maintenance activities, ensuring that resources are used efficiently and effectively without compromising on quality or safety standards.
In addition to saving time and money, predictive maintenance gives peace of mind knowing that equipment will operate as expected when needed most.
Cost Savings from Avoiding Unplanned Downtimes
Unplanned downtime can be a costly and frustrating experience, especially when it comes to field service management software. Fortunately, predictive maintenance solutions allow businesses to identify potential issues before they arise and save both time and money in the process.
Predictive maintenance strategies are designed to analyze data points that could lead to unplanned downtime, allowing businesses to take proactive steps towards avoiding such situations. This can result in cost savings from reduced labor costs as well as decreased operational costs due to fewer instances of unexpected down-time or repair needs.
These savings can help businesses maintain their bottom line while ensuring customer satisfaction by preventing disruptions in services provided.
Proactive Maintenance Planning and Scheduling
Proactive maintenance planning and scheduling is an essential factor for effective predictive maintenance in field service management software. By taking a proactive approach to routine upkeep, organizations can ensure their equipment and systems are running smoothly and efficiently at all times.
This helps reduce the amount of costly downtime due to mechanical or technical issues that could have been prevented with proper preventive maintenance practices. Through proactive planning and scheduling, technicians can be sent out ahead of time to detect any potential problems before they become an issue while also allowing them to plan around existing customer demands or business needs.
Additionally, having detailed records on each piece of equipment enables teams to maintain accurate inventory levels so they know exactly what parts need replacing when something does go wrong – saving further money in the long-run by avoiding unnecessary part purchases or replacements. In summary, proactive maintenance planning and scheduling is a key component for successful predictive maintenance strategies within field service management software.